

Posts Tagged ‘Space:1999’
Space: 1999 Models: New 1/72 scale Eagle kit Pt. 7
This post finishes up the preview look at our new 1/72 Eagle kit. As things stand now, we have gone through three rounds of test shot refinement, the box art is done and production will begin soon. The kits are on track to be in the market in November.
Paint: The Final Frontier
Oops! Wrong show. Carry on.
By E. James Small
First, I apologize to readers for finishing this up so late. Life and other jobs took priority so I just couldn’t put it to mind until those chores were done. Anyway, we continue with where we left off.
After all sub assemblies are done it is time to paint the model.
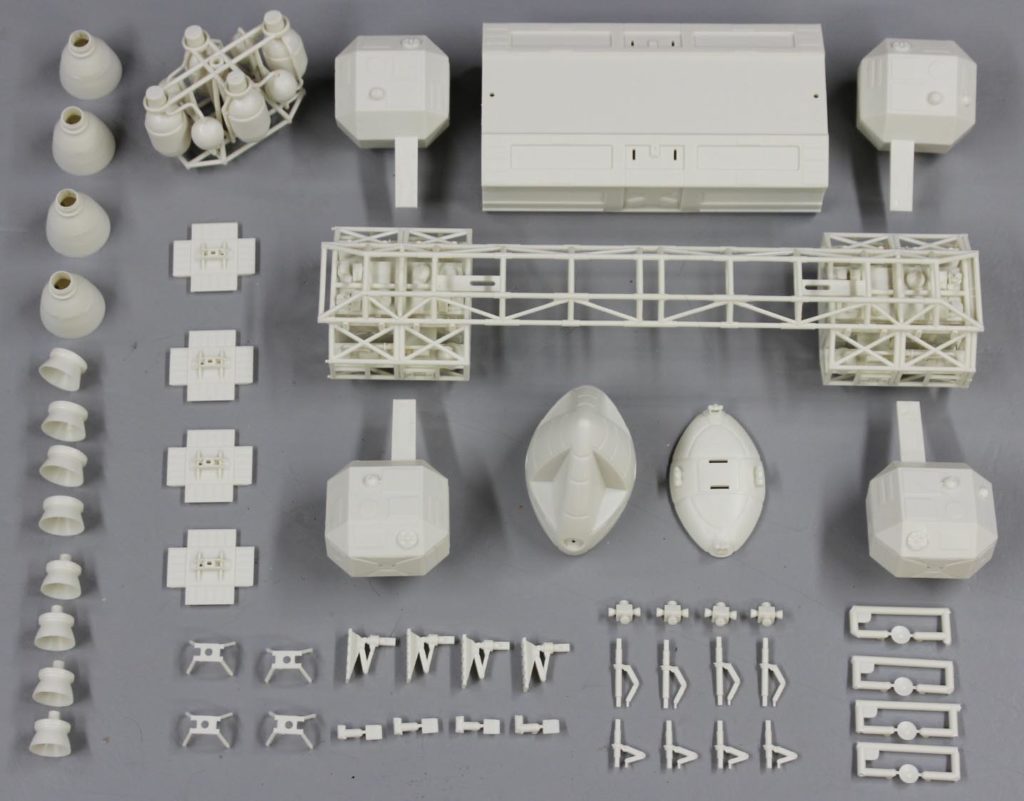
I first used gray primer to paint all parts, straight from the
rattle-can. Then when the gray primer was dry I primed it again with
white. Why two primer coats? First, the gray primer is much more opaque
than white primer is. And primer is much less physically thick than the colour
coat. By priming it first with gray to knock back the translucency of the
plastic and then putting white (which covers better than colour coat) over
that, it makes it possible to use a lot less of the main white colour coat.
The off-white colour coat was then sprayed over the white primer. I like to use
automotive lacquer when I can because it dries very fast, is very tough, and
goes on less thick and less likely to run than enamels or most acrylics or
alkyds. When lacquer dries, most of the carrier evaporates and the paint
pigment hugs the details very well.
Details were either left in primer gray or sprayed black and silver as shown.
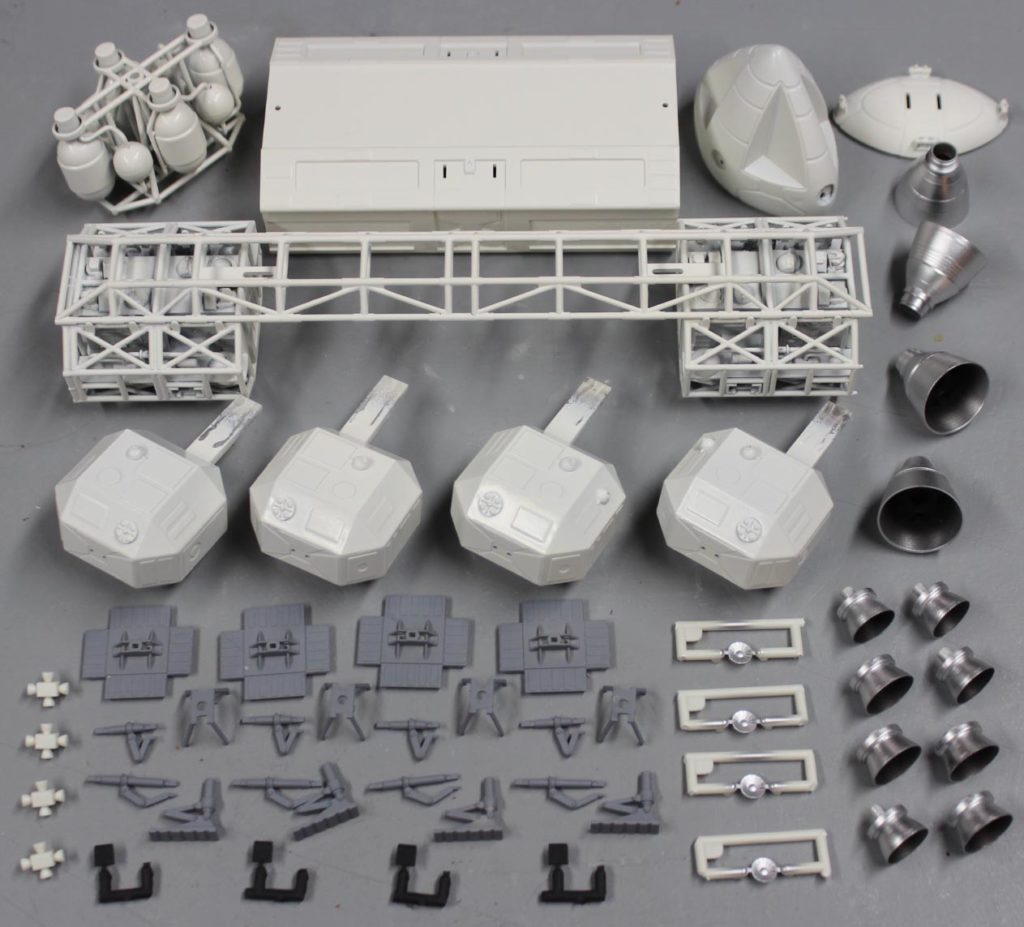
Weathering was done by first cutting chunks from an old business card and using it as a soft mask to airbrush light gray paneling effects over the entire model. This method is very fast, easy and looks authentic because they often used this technique on the original studio miniatures as well.
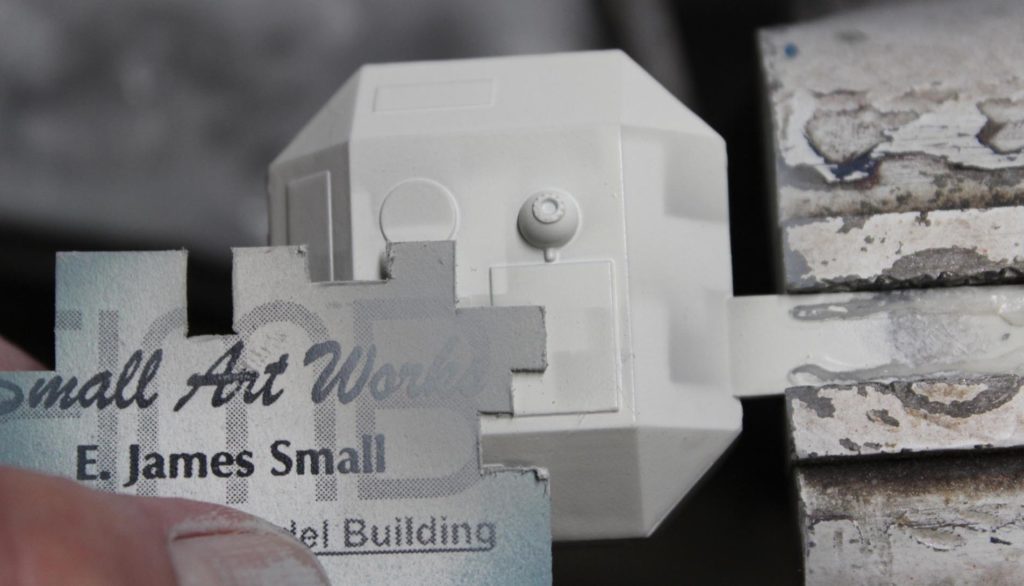
Further weathering was done by dusting some black powder paint over the model then wiping or blowing off the excess. Black powder paint is gray unless you add water to it. This allows the details to pop a little more.
Now it’s time to paint the details and add decals.


The landing gear oleos’ silver struts were just hand painted.
Those of you who need more attention to detail and more time to spare would do
well to cover those struts with Bare Metal Foil for an even better appearance.
The landing feet “toes” were dusted with a lighter gray. Since the actual kit
decals had not been done yet, I printed a set myself by using scaled down ones
from the previously released 22” Eagle also available from MPC/Round 2. I find
that using “Future” floor coating applied to the model just before the decal is
applied gets rid of a lot of silvering and saves having to spray the entire
model with a gloss coat, as decals never work well over matte surfaces. The
Future blends the decals into the surface. Just apply the Future to the surface
a few seconds before you apply the decals.
Finally the entire model, minus the silver bits, was sprayed with dull coat.
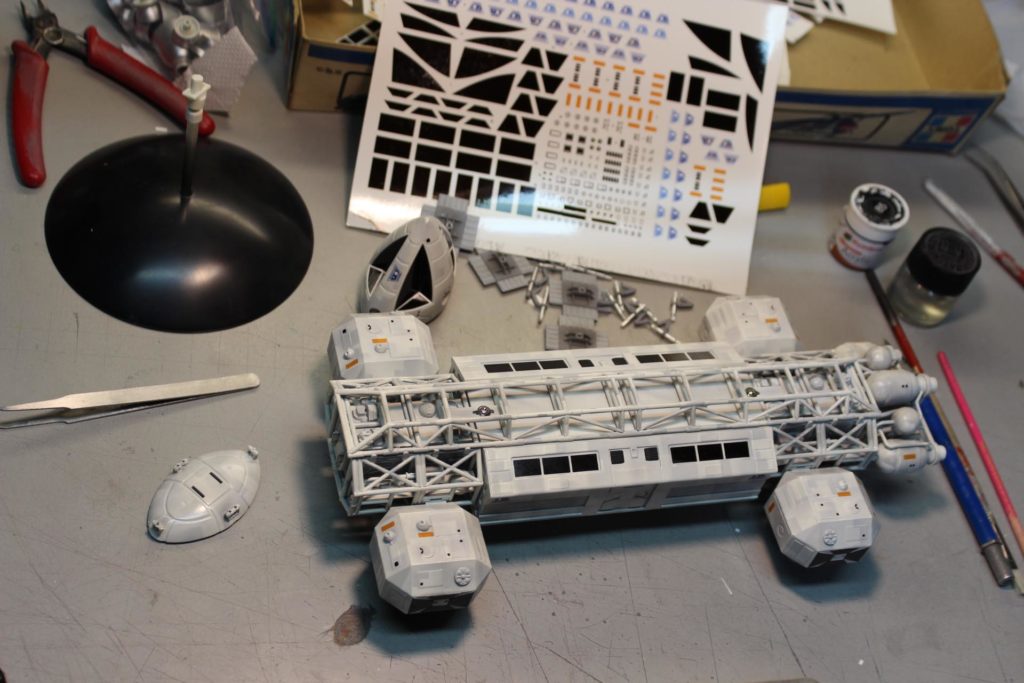
Here are all the painting products I used to finish the model.

Left to right: Generic Canadian Tire gray primer, Krylon white primer, Dupli-Color off-white automotive lacquer, Krylon Chalky Finish Misty Grey (for the airbrushed weathering), black powder paint for weathering, Krylon Chalky Finish Matte Sealer for the overall finishing dull coat, Krylon silver for the engines and finally Rust-Oleum Quick Color flat black for airbrushing inside the engine bells.
Why use spray cans instead of hobby paints, you ask? Because of the expense, mainly, and convenience. There are no hobby shops near me and spray cans like these are readily available at local hardware stores. Also you get a lot more paint for the money with spray cans and at the rate I go through paint it would cost me a fortune in hobby paints for my work. I do have a stash of hobby paints that I have collected over the last few decades (usually Tamiya, with some Testors and others) used mostly for small detail brush work.
Then came the photography of the model for the box art once the painting was all done. Jamie Hood did a GORGEOUS painting (Wait ‘til you see it!) for the main box art but we needed pictures of the model for the rest of the box and tray. Most of it was all just standard stuff shot against a black velvet backdrop but I wanted a “hero” type shot showing an environment for the main box tray picture. Jamie picked out a shot from the show itself that had the angle he wanted, so I just more-or-less copied that shot using the 14” model in place of the original 44” VFX miniature. I painted up a quick and dirty partial launch pad to scale from an old board I had laying around for the model to sit on so that shadows cast onto it would look natural. That was better than just Photoshopping the model onto a digital background. Besides, even though this was to be a manipulated shot and a composite, I wanted to use real physical elements wherever possible. Real objects always look better than computer generated ones. Knowing the angles necessary I didn’t need very much of the pad to show, that’s why it’s mostly unfinished and all chopped up. Took just a few minutes with a couple of spray cans to make.
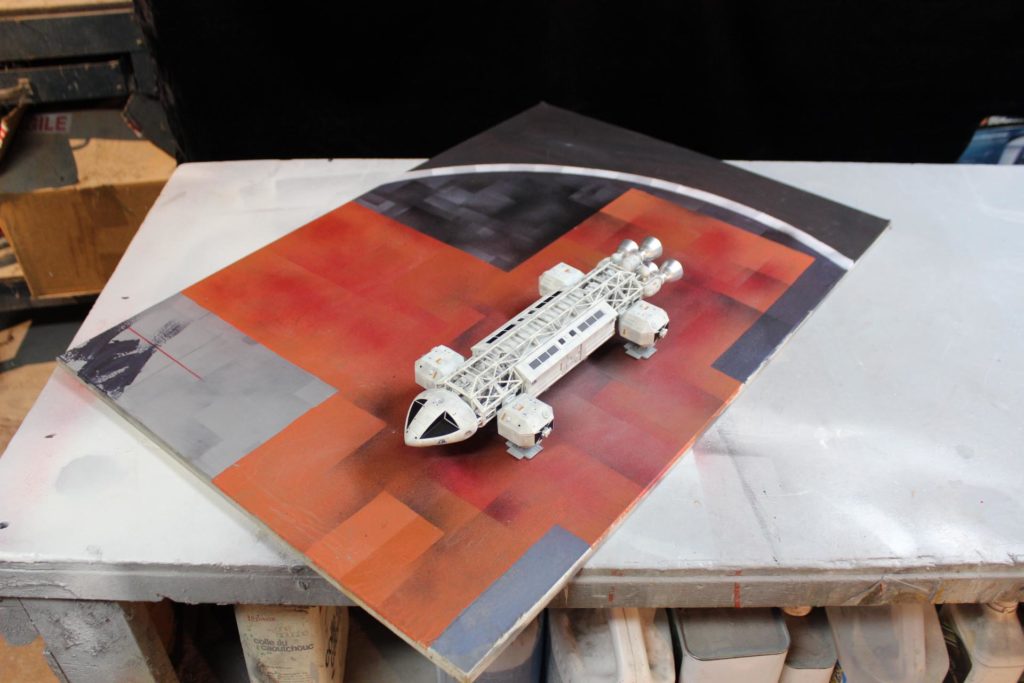
Then when strategically lit to look somewhat dramatic it was photographed then brought into Photoshop where I matted in a background of the Lunar surface using elements I had made from the 22” Eagle Cargo Pod kit box art. The mountains are just bits of foam chunks and tin foil sprayed with gray primer, covered in cement dust for texture and shot up close with appropriate lighting. The mountains are only about 3-5 inches wide or so.

Looks pretty good and reasonably well matches what was seen on screen. Only thing I’m not happy with are the launch pad lights. I didn’t have the time needed to wire in real lights on the pad set so I just digitally plopped those in quick. I’m not the artist in Photoshop that Jamie is though. Maybe he can make them look a lot better by the time he lays out the box art. He can probably improve the entire scene as I did that composite rather quickly, I had other work to get to.
I hope you people out there will enjoy this new kit. It is amazingly well done for its size and has all the external details of the larger 22” model but takes up less space for those of you who don’t have much room to spare. Another fantastic achievement by Jamie and his gang over at Round 2!
We can’t wait to see what you all do with yours!
Jim.
Space: 1999 Models: New 1/72 scale Eagle kit Pt. 6
If you think you are experiencing deja vu, it isn’t just you… This post was published in error earlier. Here it is again following the correct order. Continuing our guest series reviewing the new 1/72 Eagle test shots. Enjoy!
Getting Ready for Paint!
By E. James Small
OK folks, here we are on the home stretch before we break out the spray cans and air brushes!
If there is one part of this model that is the most confusing, it’s the shoulder pods. Yes, they are simple to build, but really easy to screw up parts orientation, so if there’s one place where you REALLY have to pay close attention to the instruction diagrams, it’s here. These are the assemblies that you triple check before applying glue. I’ve even seen some of those lower cost “pro” builders get that stuff wrong on the larger 22” model! Meh, you get what you pay for I guess.
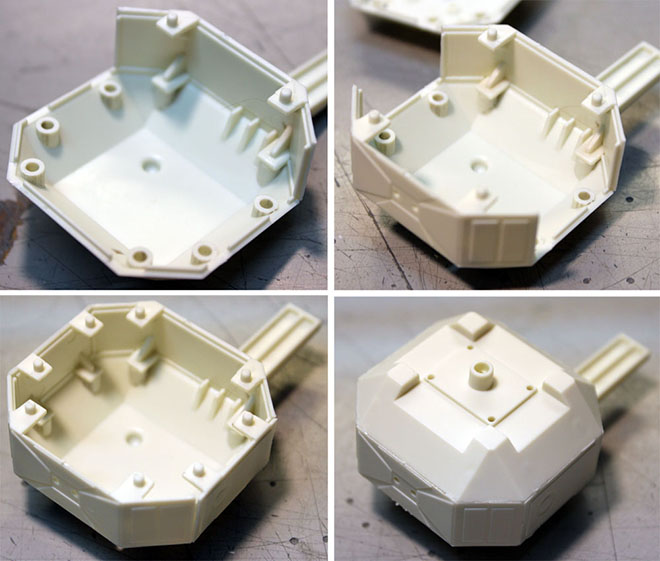
First you need to understand how the detailing on the pods work on the Eagle. Note that the pods are mirrored front to back and side to side. In other words, the detailing on the pods left to right are mirrored from each other and the details between the front and rear are also mirrored… except for ONE detail…
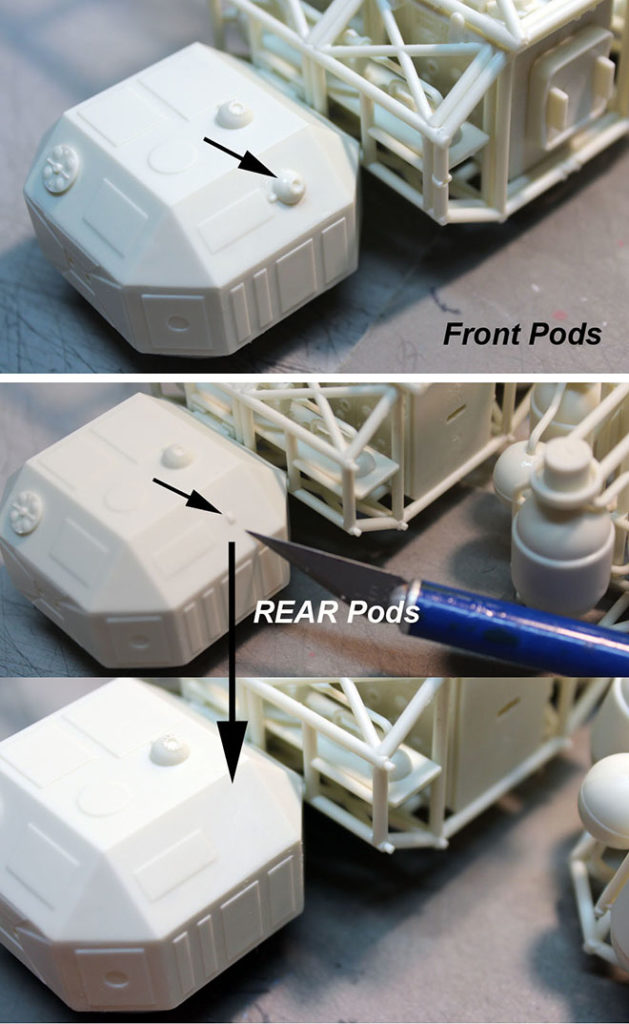
Note that the little dome shown by the arrow on the front pods are left off on the rear pods, so you’ll need to carve or sand off the little locator tab on the rear surfaces as shown. Of course, if you WANT to, you can also put domes on the rear pods too. It’s just that they were left off on the original for some reason. The footpads are two pieces and simple enough but there is a seam/joint running around the bottom that needs to be filled in and then, when putty is fully dry, sanded down.
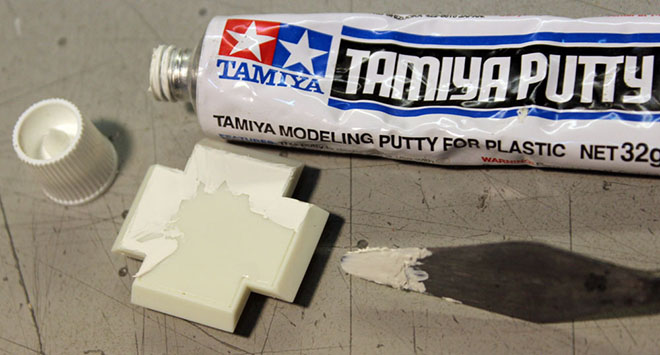
The nosecone assembly is best handled like this:Put the two main halves together, dry. Then using water thin liquid cement, touch a few drops along the joint, allowing the cement to “wick in” and get carried along the joint with capillary action. Then, after the solvent has worked at melting the plastic for a few seconds, firmly press the two halves together, making he plastic/solvent squish out the sides. DO NOT WIPE IT OFF. Allow it to dry like that overnight. Then, when dry, you can sand down the joint nice and smooth and no puttying is needed. Most joints on the kit can be handled this way. The footpad bottoms, as above, seem to be the only exception.
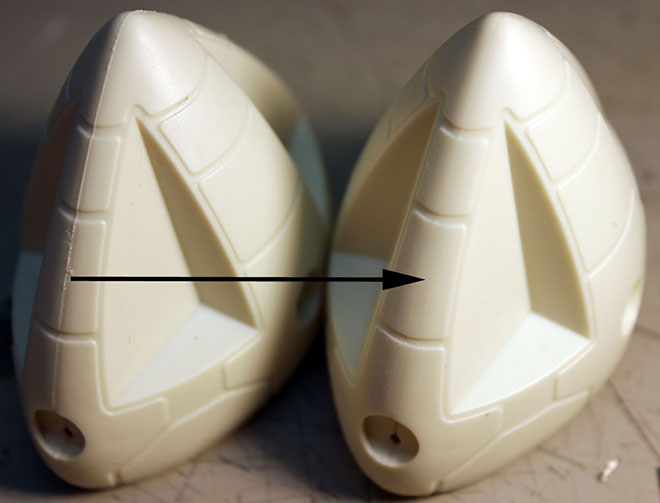
Now glue the nosecone clamps to the back of the nosecone section. Before the glue sets, offer the assembly to the front cage section to make sure the pins locate properly to the holes in the frame.
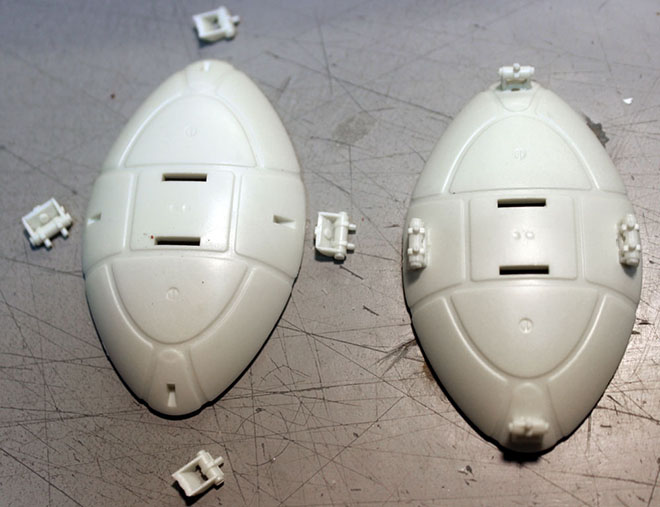
Now glue the frames to the spine (watch orientation!! Doors on cage boxes point towards each other!) and you should have all the subassemblies as shown in this final picture below. Some parts, such as the little sensor dishes for the nosecone and the black ribbed bits for the top of the Passenger Pod doorframe are left attached to the runners for easier handling when painting. Do what is easiest for you. I left out the assembly procedure for some of the simpler parts like the engine bells as that should be a no brainer. Clean up any unsightly seams etc. following standard modelbuilding procedures. At this stage you are ready to begin painting. That will be covered in a later post. Stick around!
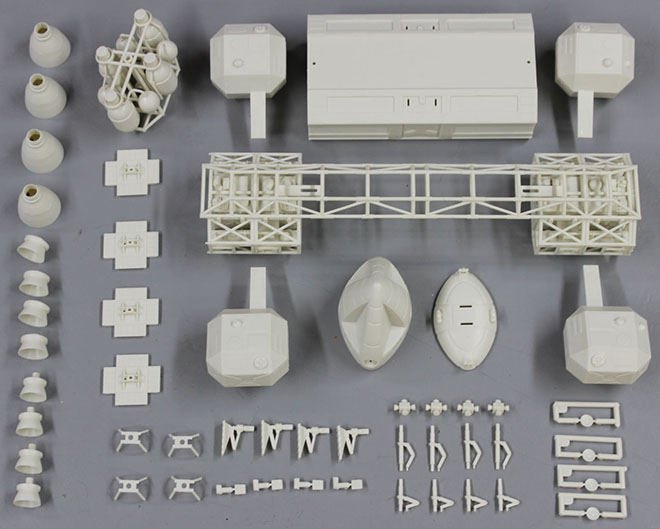
Space: 1999 Models: New 1/72 scale Eagle kit Pt. 5
Welcome back! Your eyes do not deceive you! This continues our guest series reviewing the new 1/72 Eagle test shots. Enjoy!
Engines of Construction.
By E. James Small
For many people, doing this engine assembly might be the trickiest part with all the piping and so forth, but if you follow this procedure, you will find it actually pretty easy. First grab the octagonal engine mounting main frame and the four supports with flats as shown. Glue them in place, making sure the flats (tinted red in this photo) point toward the centerline of where the top and bottom engines will be mounted. See arrows.

Next glue the cruciform section in place.

Then with the glue still soft, cement in the four angled braces as shown. Do two opposing corners first, then the other two. It’ll do a lot of wobbling around on you as you do this, but you will find that once all of the braces are in place everything will self-align. Put the unit down on the table as shown and press down gently on the center of the cruciform to weld everything together for a strong bond. Make sure the cruciform is not twisted in relation to the main frame when you sight straight down on it.

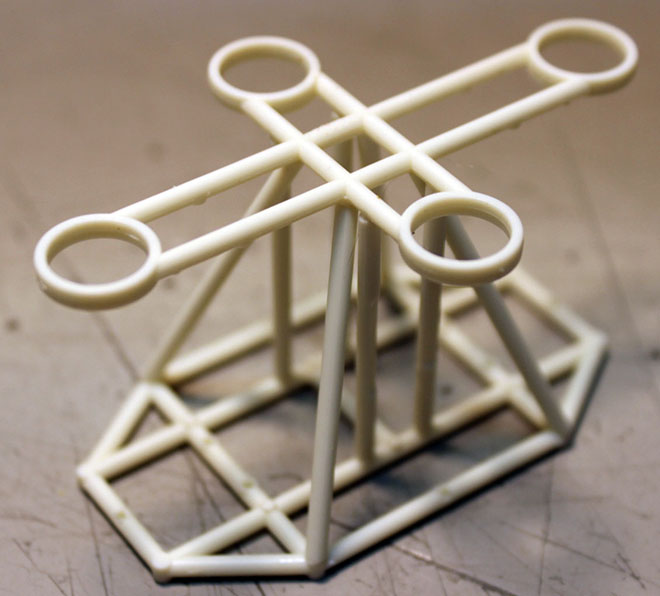
Next assemble the sphere halves onto the sphere frames and then glue those assemblies in place between the main frame and the cruciform as shown. It’s easier to put the end onto the main frame first, then swing it up into place in the cruciform. You can flex the parts just enough to allow the pins to clear.
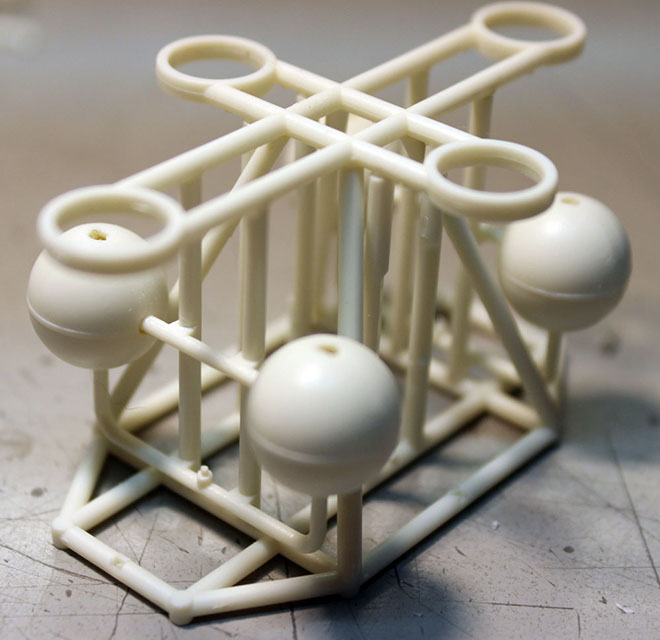
Now, grab the longest of the squiggly pipe parts and glue them to the main frame as shown exactly in the picture. It’s the same on both sides. Tweezers will help a lot here. Pay close attention to the orientation of the parts, exactly as shown. Just glue the center down on the pin in the middle and make sure you sight it all up and keep the tubes level and parallel as shown. Allow to dry.
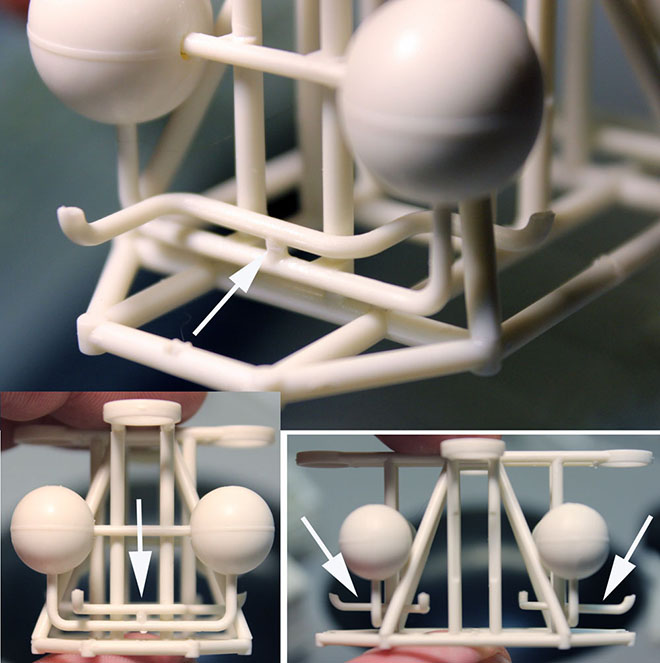
Now you can put the main engine bottles into place. Push the back ends through the cruciform hoops first, then swing the front pins down and cement them to the main frame. Line up the piping so they fit with the previously placed squiggly pipe sections and glue the joints together.


Glue on the remaining piping that goes from the spheres to the back of the engine bottles.
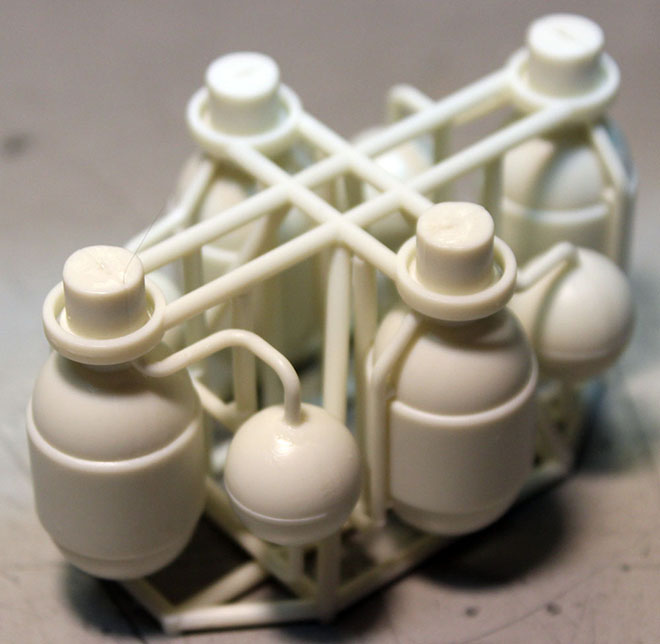
Now you can also put in the center pipe that goes from the center of the cruciform to the main frame. Make sure it is centered and seated as shown. You can offer the assembly up to the rear of the cage assembly to make sure it all lines up before the glue dries.

And you’re done that section! That wasn’t so hard, was it? You can either glue it to the back of the cage assembly now, or you can leave it of and paint it all as a unit. Enjoy! More to follow…
Space: 1999 Models: New 1/72 scale Eagle kit Pt. 4
Continuing our guest series reviewing the new 1/72 Eagle test shots. Enjoy!
Getting Cagey About This Build.
By E. James Small
Here we go again folks. Another update on the 1/72 scale Eagle build.
This one is pretty simple despite the complicated way I’m describing it. Just showing my personal recommendations of the building sequence for the cages on the model. In my opinion this is the best way.
Procedure is the same for both end cages of the model.
First, assemble the 4-part companionway “box” sections with doors and 2-part shelves. Make sure you get the roof oriented front to rear as shown and door oriented properly top and bottom!!!When you glue on the shelves, make sure you get them as close as possible to the box structure and make sure they are dead on parallel with it to make sure the rest of the cage frame structure will glue properly in place.
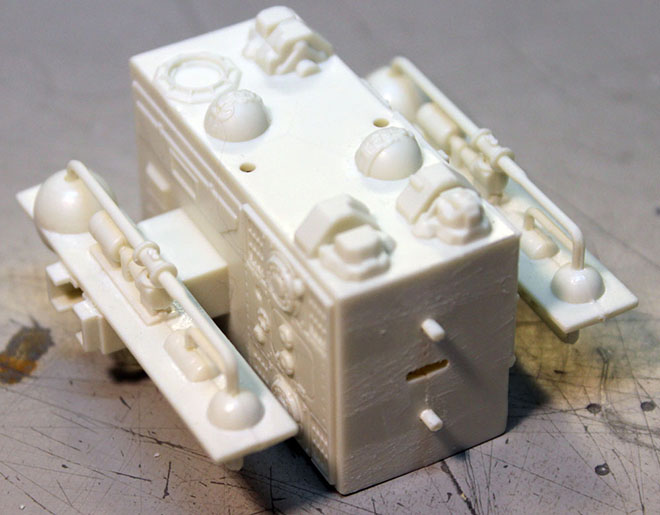
Next, glue on the TOP cage structure as shown. Make sure it all stays perfectly parallel. Make sure you glue it on the right way ‘round too! Note that the little locator pins on the end of the longitudinal pipes go to the same end as the slotted end of the box, opposite the doorway as shown!
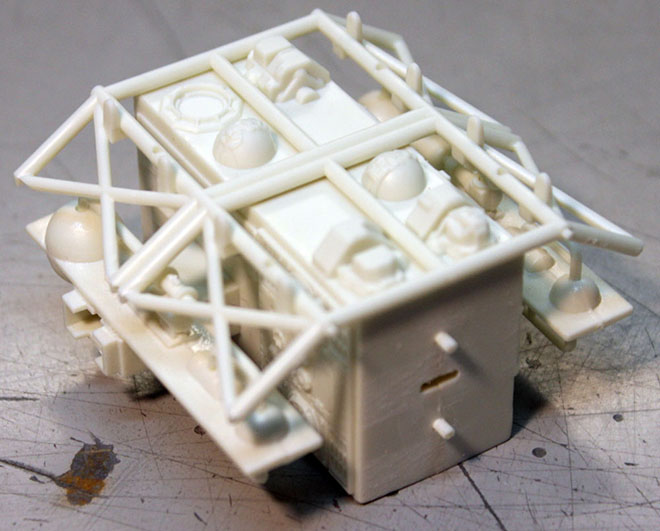
Next get the notched uprights on either side of the boxes as shown and glue the ends ONLY to the top cage section. Tweezers or fine pliers will help a lot in this operation. Make sure the notched sections of the pipe go flat against the shoulder pod plug-in sections as shown by the arrows but don’t glue the flats in place yet!
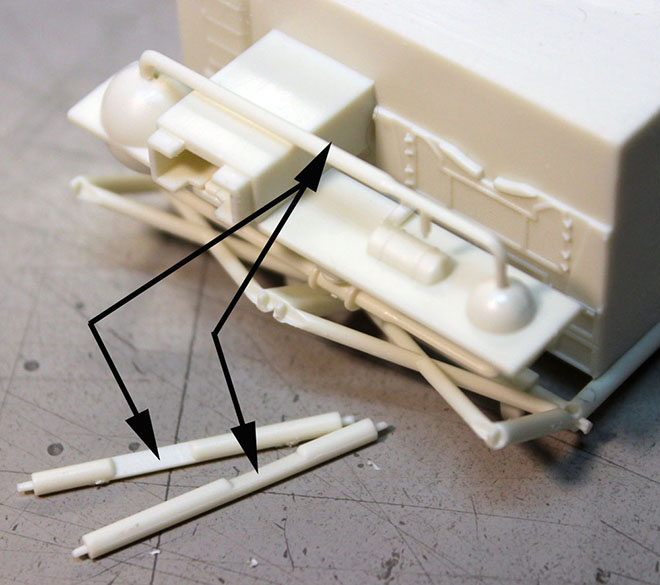
Glue the non-notched uprights next to them.
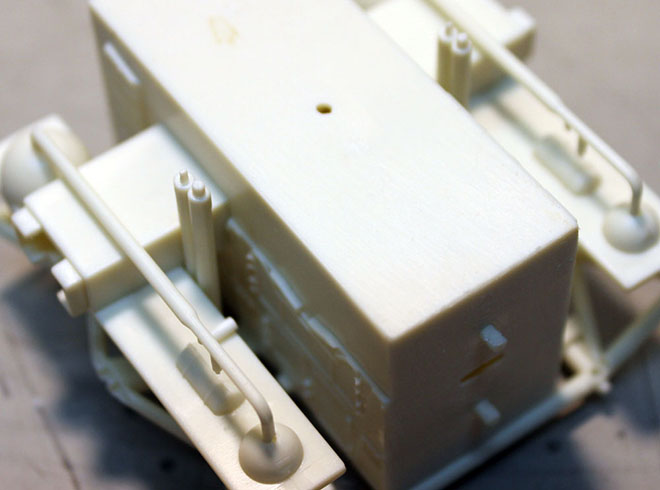
Next, you will carefully orient the bottom cage section (pay attention to those longitudinal pipe end pins again!) and line up the ends of those pipes to the holes and glue in place at those joints only. Yes, it’s a little sloppy right now and things can still move but that’s what we want at this point. We want to allow for a bit of movement until we get the side frames in place as this will assure proper alignment.


Next glue the end uprights in place by carefully flexing the top and bottom frames to allow the pins to be inserted.
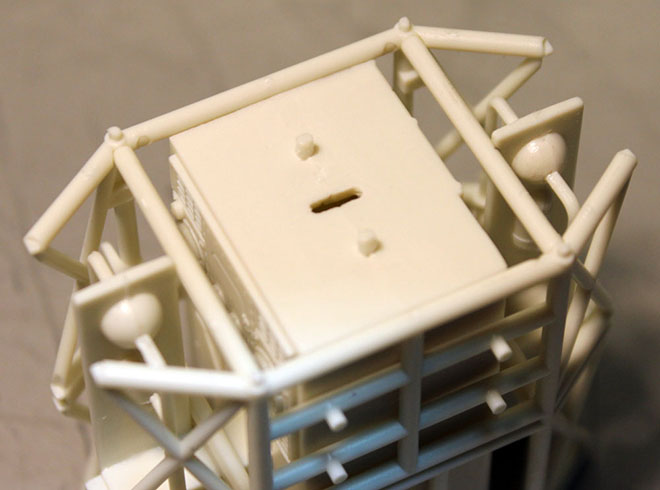
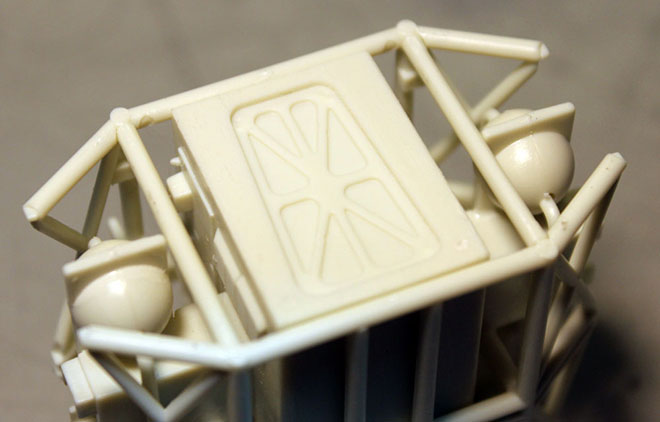
Now you can glue the side frames to the top and bottom frames. Once those are in place and carefully aligned you can use a long brush and liquid cement to glue the rest (flats on uprights and bottom frames to boxes) in place.
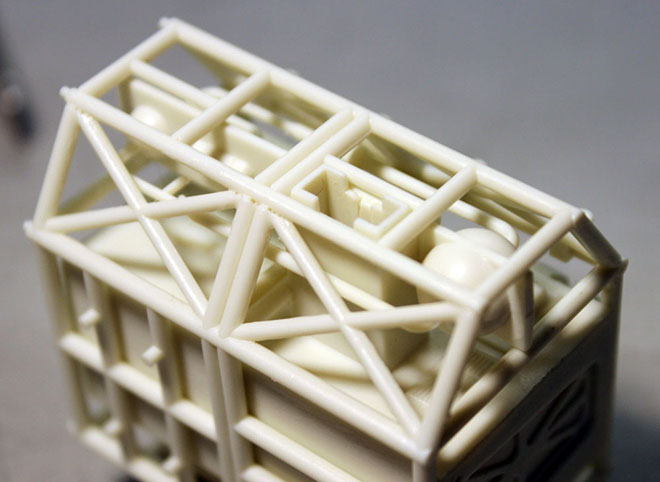
Lastly you can glue the front octagonal frame and nosecone mount in place.
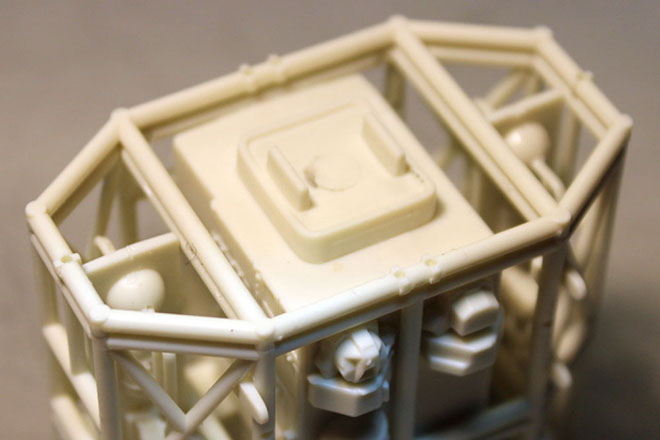
You can test fit it of course, and it is recommended before the frame glue dries, but DO NOT glue on the REAR octagonal engine frame yet! You will need that separate for when you build the engine section. That frame will be put in place only after the engine section is built! More to follow….
Space: 1999 Models: New 1/72 scale Eagle kit Pt. 3
Continuing our guest series reviewing the new 1/72 Eagle test shots.
Let’s Prep for the Future!
By E. James Small
Ok folks, when you build your new 1/72 scale Eagle, you’re going to want to think ahead. What if you need to add something later? What if a cool new optional accessory like… oh, I don’t know… say, a side booster set or something similar gets put on the market? You’ll want to access the inside of the passenger pod so that such an option can be attached with magnets, so you don’t have to glue those accessories to the pod permanently. Access to the inside will allow you to do so at a later date. Therefore, when you build the passenger pod on your Eagle, you might want to do it in the sequence shown…. (same goes for the 22” model too, frankly speaking!)

First assemble one side and end wall.
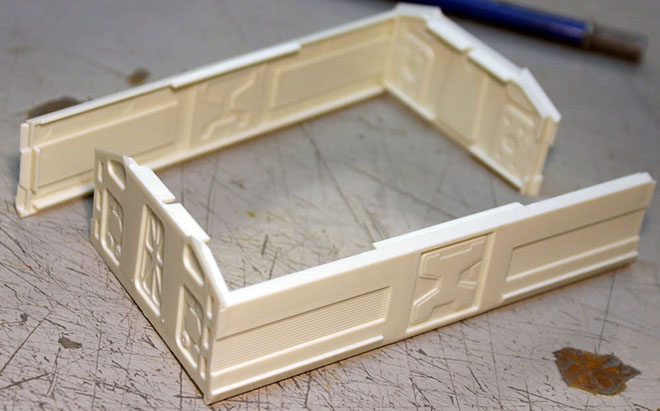
Then do the opposite two.
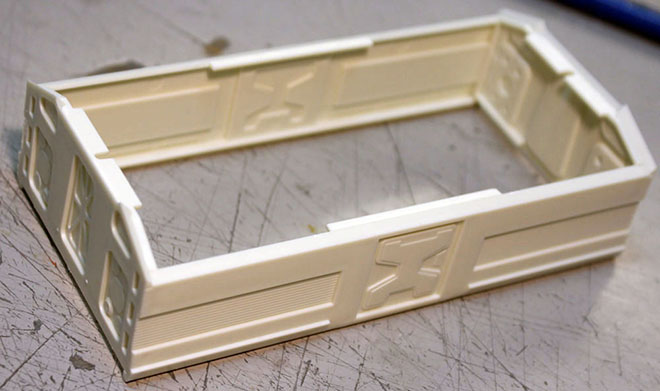
Then lastly add the roof.

Sand down the seams as needed. (Hint: Leave those two little square ribbed bits that go above the door off until your model is painted… much easier to paint them black separately and add them to the pod after you have finished all your painting! That’s why they were made as separate parts, and why they are not shown here!)
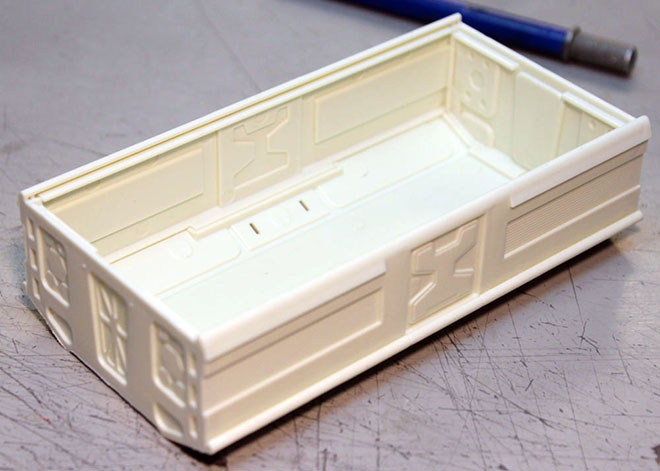
Put the floor on LAST! Why? well, before you put the floor on, you may want to consider allowing it to be removable so the inside can be accessed later as I mentioned above. You can do this by attaching the floor using magnets or screws. Yes, you’ll need to add something of your own design, such as gussets attached to the inside corners for the magnets and screws to mount to. So go ahead and devise your own way of making that floor non-permanent.
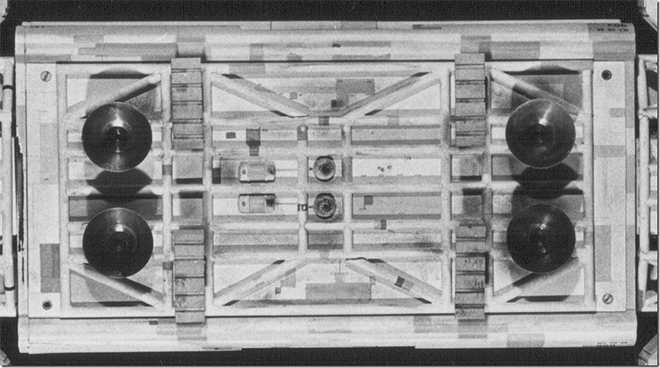
If you are careful when gluing your passenger pod walls together , you may find the floor to be a natural friction fit as well. so you may decide you don’t need magnets or screws, but don’t count on it. Friction fits are not always reliable.
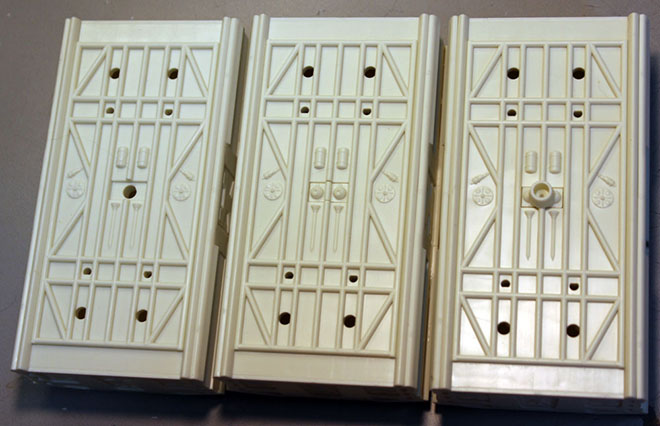
As you can see, the kit as it comes allows for the stand mount to be optional as well. By making the floor removable, that small centre bottom hatch can be more easily replaced if you want to swap them out as desired. See the three pods side by side? The hatches shown are most easily removed by pushing them out from the backside of the floor. By making the floor removable, you can make your model a lot more versatile! Heck, you could even get adventurous and put a lighting power supply and switch in there if you want to modify your model for lighting! So keep this in mind when you build your Eagle! Enjoy!
Space: 1999 Models: New 1/72 scale Eagle kit Pt. 2
Continuing our guest series reviewing the new 1/72 Eagle test shots.
Also, we have posted photos on our facebook page of every entry that was eligible for our award at Wonderfest USA last weekend. We also posted a short video of the four adult finalists.
Enjoy!
Developing a Spine in Today’s World.
By E. James Small
One of the things I personally worried and spent a lot of time thinking about when contemplating the shortcuts needed to take the fantastic MPC 22” Eagle and shrink it down to 1/72 scale was how the new model’s SPINE was going to be molded. We didn’t want it to look like previous versions made at similar scales that had flat backsides of the tubing and still be strong enough to support the finished model. Also it had to be ACCURATE in proportion as well as easy to build. Parts count and tooling real estate had to be kept to a minimum to keep costs as low as possible. Tooling draft, which means that the two halves of a solid steel mold must be able to be pulled apart without trapping plastic parts in undercuts that would otherwise provide full detail, has always been a problem for all injection kits. That standard had to be improved upon so that the new model would still represent the original HERO miniatures and not look like a cheap toy. Previous offerings of die cast and injection molded models and toys all had those problems. Therefore, how to do it better?
This is one of those times when I wish I could satisfy my personal ego and take credit for such a simple yet ingenious solution as shown in this picture.

Nope, can’t do it. I had nothing to do with it. The design credit goes entirely to Round 2’s graphic artist and product developer Jamie Hood! In fact it’s one of those Homer Simpson “DOH!” moments when Jamie showed me his idea and I thought to myself “DUH! Why the bloody hell was that never done before? It’s such an OBVIOUS solution to the problem! Why couldn’t I think of that? Why did nobody else think of that decades before?
And, no doubt, all of you reading this, now having seen it will also say the same thing and think; “Why would you do otherwise?”
OK, ask that question of everyone else who made an injection molded Eagle model. Let them wallow in the failure that has been overcome in this new kit! Get it? Yeah, easy to understand once you see it done, not so easy to come up with that simple solution if you’ve not already seen it! Jamie is fairly reticent to take credit for a lot of stuff he does, including the many illustrations he does on kits you do and don’t even know about, so I’m gonna do it for him. Everyone please give him a virtual round of applause for his work! He does a lot that nobody hears or reads about!
“OK”, you ask, “Why wasn’t that done on the 22” model”…? Well, even with Jamie’s ingenious design that even the factory didn’t figure out, there are some flaws on this smaller model that was overcome with more parts on the larger and more expensive version. You must understand the limitations of injection molding, especially the aforementioned draft. The worst of them is slight “webbing” around the tops of the triangular bracing at the top longerons of the spine. Yes, those are necessary molding shortcuts that are needed to keep parts count and tooling down for a smaller scale and lower cost kit. As a builder you can either ignore them or take the time with a #11 Xacto blade and carefully carve them out. The point is, the model will still look “right” whether you choose to do that cleaning up or not, as shown in the photo you see here. No significant cleanup was done in the examples shown.
Ladder and frame. That’s all there is to it. Now you see what it takes to develop a good solid spine in today’s plastic world!
Round 2 Models: Wonderfest 2019 preview
We are excited as always to participate in the Wonderfest Sc-Fi modeling show each year in Louisville, KY. This year is no different and the show is just a few weeks away. You can check out specifics on the show here.
Don’t forget that each year we award participants in the model contest for the BEST USE OF A ROUND 2 MODEL KIT! There is plenty of room for interpretation in that definition. We like CREATIVE use of any of our kits, but if not that, then over-the-top craftsmanship usually catches our eye. Use our kits in an exciting way in a super-clean kit-bash, and you’ve got yourself a winner! We present awards for adults as well as models from the child or youth category to encourage young talented modelers
We are preparing our booth display where we’ll show buildups of our most recent and upcoming releases as well as sneak peeks at some new stuff. We usually try to keep the wraps on things until the show, but a few of our upcoming new kits were recently placed on our distributor price list. So rather than let everyone try and figure out what is going on, we’re going to fill you in NOW!
We will be showing three new sci-fi/pop culture kits at the show this year starting out with the 1967 Impala from the popular series, Supernatural. We’ve gotten a ton of requests for it and its as iconic a car as you will find on the airwaves today. We will have a mockup on display at the show.
We have been reviewing test shots that will be used in this year’s Space:1999 prebuilt product… drumroll, please… a 22″ Eagle II. The model will feature a slightly different engine bottle arrangement and all-new shoulder pods. The springs will be a bit “softer” to compress more fully as we see in the show. Just showing some pics of the assembled test shots isn’t that appealing, but we intend to have a fully factory-decorated piece at the show to show off exactly what the final product will look like.
Lastly, (but not leastly) we will be showing a fresh test shot of our brand new tooling of the 1/72 scale Eagle. At 1/72, the ship measures little over 14″ long and will eventually replace the old 1/96 scale MPC model everyone is used to. It will be the first model of the Eagle to ever come with a base to hold it in flying position. We’ll drop a ton of pics here with some comparisons to our other models. We hope to see you at the show!
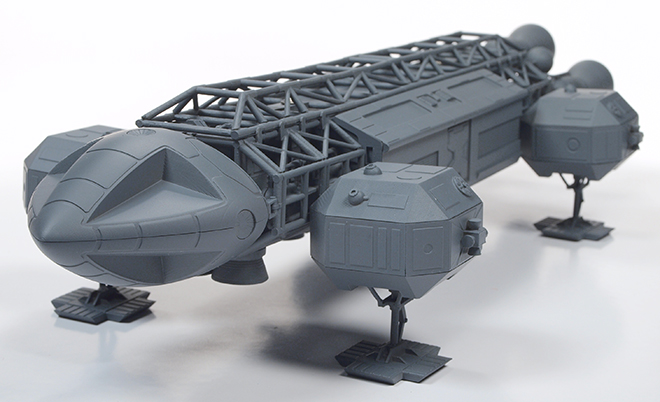
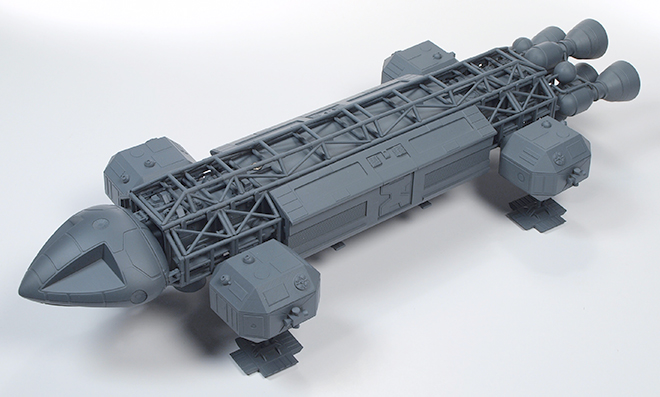
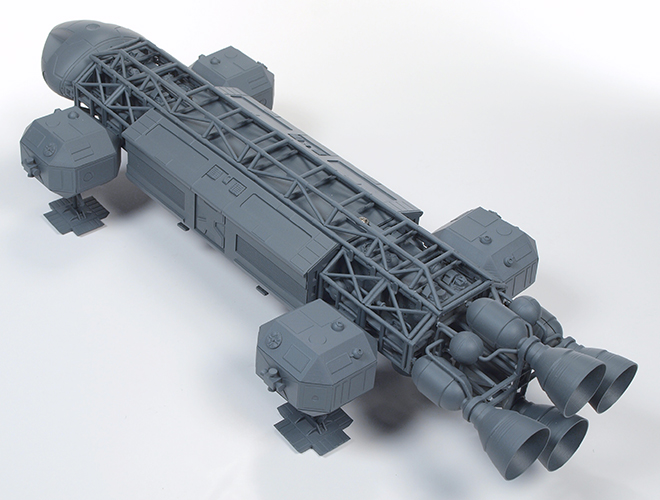
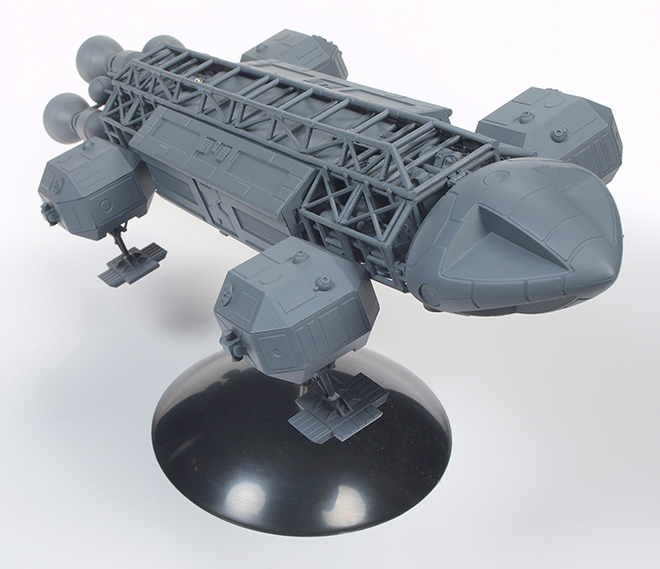
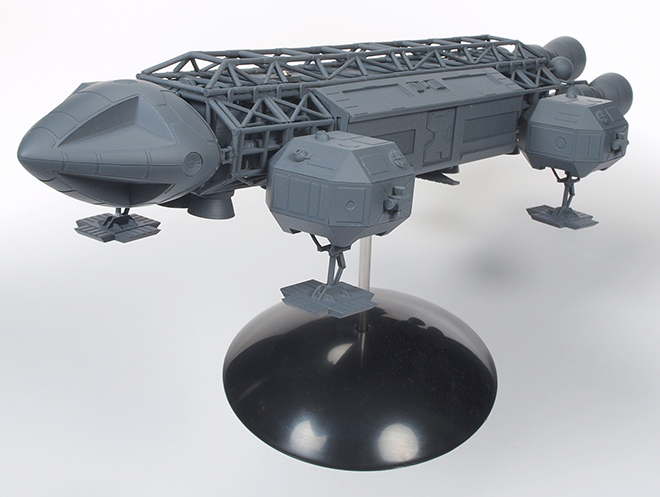
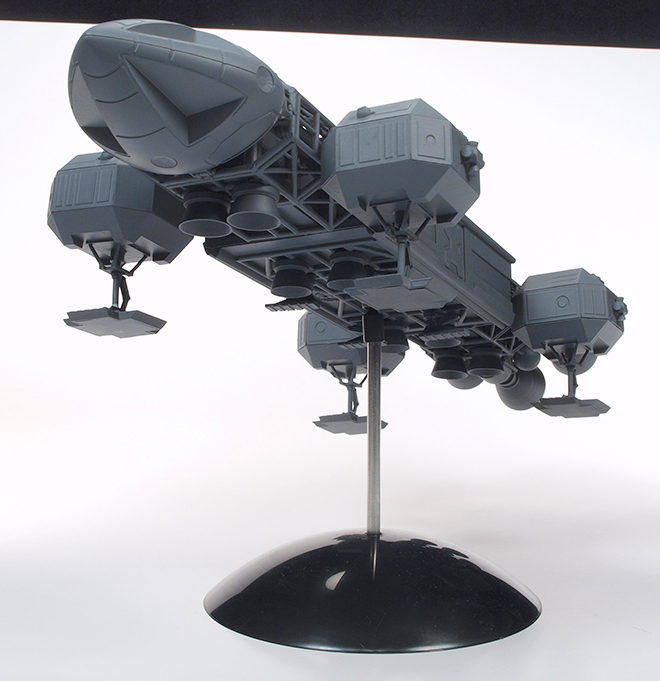
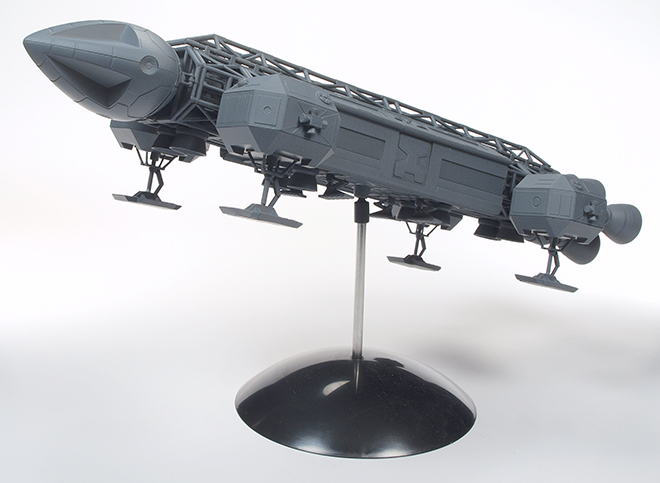

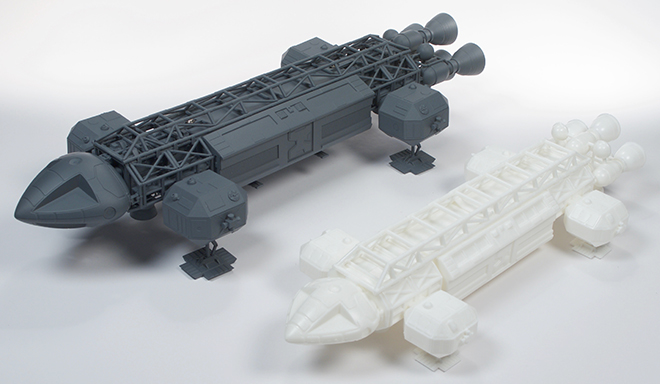
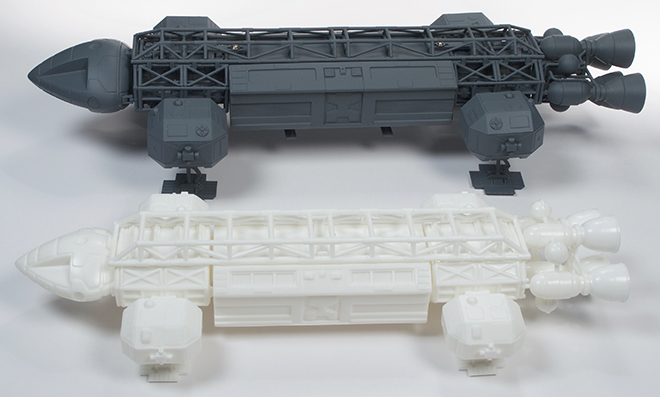

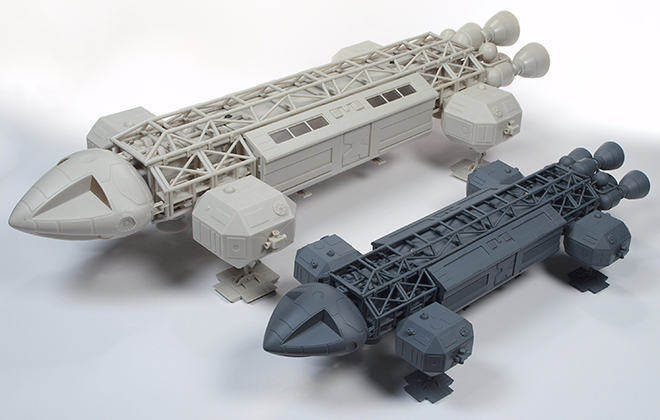
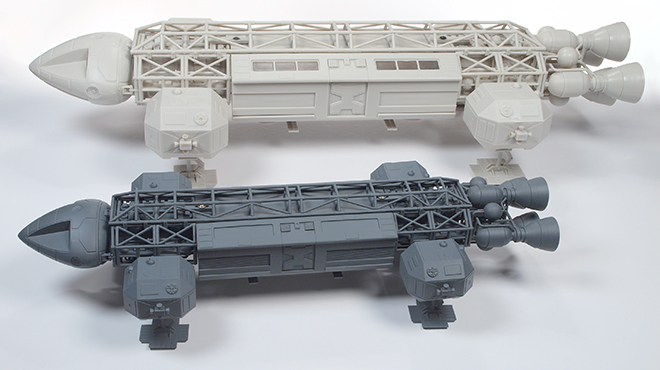
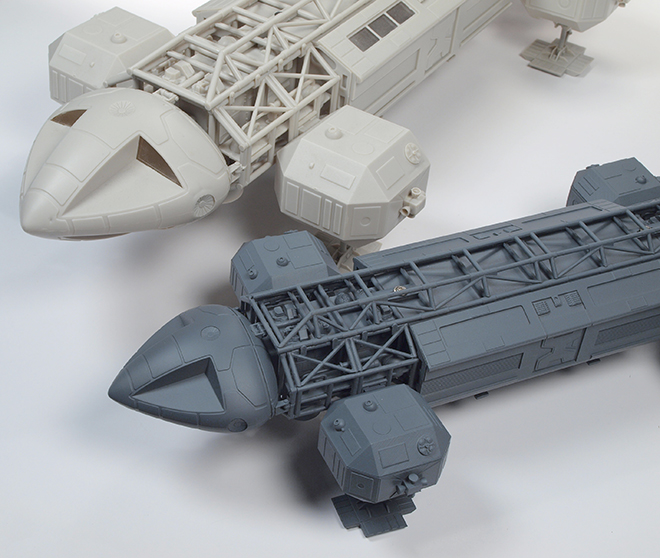
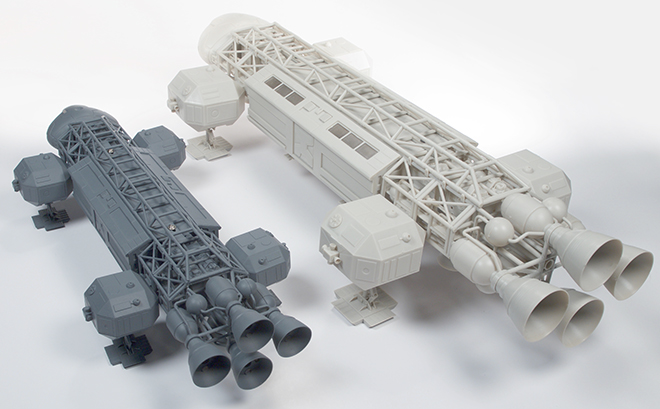
MPC Model Kits: Prebuilt Rescue Eagle Packaging
Last year’s release of our 22″ Prebuilt Space:1999 Eagle Display Model was an instant sell out. It was limited to just 500 pieces as we tired to judge the market for a fully painted and (mostly) assembled model. The response to it has been great, and as you’ve probably heard by now we are doing it again.
This time we will be releasing the model with a Rescue Pod which features its iconic red and white stripes. The weathering panels have also been changed up from last time as well. And we have bumped up our production number to 850 this time around. Pre-orders on the model have been great and we expect another sell out. We’ll see if there is still enough interest to do more later on. The model should arrive in late November or December. Here is a look at this version’s packaging.
Polar Lights Model Kits: Quick update
[UPDATED] I know it has been a while between posts and that is due purely to getting super-busy. (It happens all too often… but that’s a good thing, no?) I just received something to share that is worth interrupting my busy workday, but it will need to be quick. But while I am writing, a few updates…
POL952 U.S.S. Defiant – Arrived at our warehouse this week. You should be seeing it available from your retailers in the next couple weeks.
MKA028 Eagle Weathering Panel Decals – I totally overlooked the announcement of this. It is essentially the same sheet we included in the Brian Johnson special edition we did of the 22″ Eagle kit. These should be available in mid-late June.
MPC881 Hawk – Should be available from your retailers by the end of June.
POL957 U.S.S. Grissom & Klingon Bird-of-Prey – Due to delays in getting the test shots refined, this kit is slipping back to August. The shots look pretty good, but refining fit for a snap kit is always tricky. Packaging for the kit is being worked on now and we’ll show that off soon. We are thrilled to announce that it will feature a box lid illustration from Star Trek production designer John Eaves!
POL950 Klingon K’t’inga – Good news/ bad news … Delays in refining the CAD has caused this to slip all the way back to October. That’s only part of the bad news. The other is that this delay also pushes the test shots past Wonderfest by a few weeks. So we won’t have a fully built and painted model on display. On the good news side, the revisions were definitely worth it, because the factory was able to supply a second mockup based on the final CAD data and it has been assembling like a dream! We will have a new primered prototype with the lights on to show off at the show along with all of the buildups of the rest of our new kits mentioned above. We really look forward to seeing everyone at the show!
Now on with the thing I mentioned. A behind the scenes look at the K’t’inga nacelle tooling being created…
Space:1999 Model Kits: All-new Hawk update
I’ve been hip deep in other matters this week, but I wanted to be sure I upheld my promise to show something cool this week. You could skip to the bottom of the post if you want another clue about “what’s in the box,” but you’ll miss a closer look at our new 1:72scale Space:1999 Hawk kit box art and test shots!
Here is a full view of the Hawk box illustration followed by a closer look at the ship and the illustration placed in the context of our box face layout. The rest of the packaging is still underway.
As with all first test shots, this one DOES have some problems that will get worked out before release. The most noticeable problems are sink marks due to the injection machine not being fully primed for injection. Additionally, there are fit problems with some of the locator pins. Some parts appear to be bent, but straightened out during assembly. Here is a look at the full sprue followed by various looks at the assembled test shot. Don’t mind the mess. These builds are usually hastily assembled glue bombs. Photos of our publicity buildup will be available soon.
And as promised…